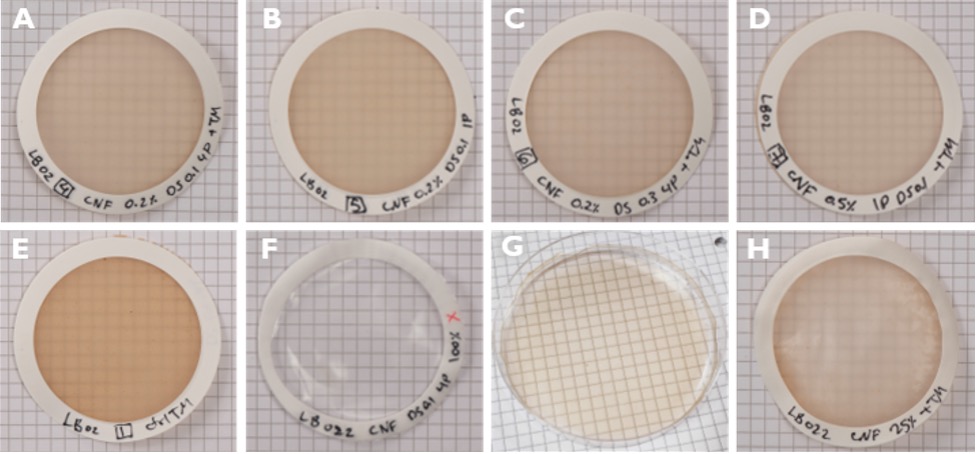
2021 Hershel Rich Technion Innovation Award
We are honored to share that the T_CODE lab has won the 2021 Hershel Rich Technion Innovation Award. The award celebrates the innovation of the Ph.D. research results of Noam Attias on and her supervisors Prof. Yasha Grobman and Prof. Ezri Tarazi on Mycelium and Nanocellulose Bio-Nanocomposite Materials.
The general aim of this research was to explore and develop mycelium-cellulose hybrids as a new type of humidity resistance packaging and hygiene product material that is sustainable, scalable, inexpensive, and uses existing pulp and paper industrial infrastructure to process and shape the hybrid material into functional products that offer clear gains compared to traditional paper or plastic-based packaging solutions.
The research focused on the development of novel sustainable bio-nano hybrid composite materials produced from an integration of, fungal mycelium and nanocellulose (NC) (Figure 1, 2). In this integrated material system, the NC acts as a reinforcing substrate for the mycelium, cueing changes in the morphology and properties of the resultant hybrid bio-composites. This work required the use of multidisciplinary tools and knowledge, with scientific efforts to understand the biological and biochemical interactions within the nano to macro scale of the material.
The research results were published in four papers (Attias et al. 2017a, 2017b, 2019, 2020). A provisional patent application that was filed in September 2020, through the Technion (TRDF 2020055). The patent opened the way for commercialization of the material in two large markets: Hygiene products – as a sustainable recyclable material for dippers and other hygiene products. Packaging products – as a sustainable recyclable material for packing that employs mycelium antibacterial properties and extends products’ life.
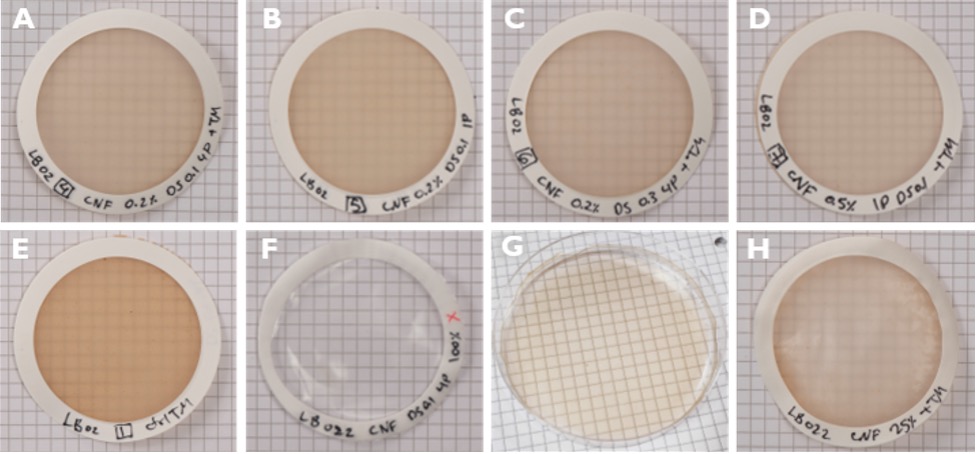
Figure 1: Hybrid mycelium-Nanocellulose films in varied conpositions. [A] Hybrid with 40% CNF DS 0.1 4p; [B] Hybrid with 40% CNF DS 0.1 1p; [C]Hybrid with 35% CNF DS 0.3 4p[D] Hybrid with 60% CNF DS 0.1 1p; [E] 100% T. Ochracea; [F] 100% CNF DS01 4P [G] Hybrid with CNC [H]Mixture (post incubation) 25%CNF, 75%mycelium; All co-incubation hybrid films result in fine and uniform materials(A-G); Post-incubation mixture is more distorted and clearly not homogenic (H).
Figure 2: Hybrid mycelium-Nanocellulose films in varied conpositions- from left to right: 100% T.ocrachea; Hybrid with ~50% CNF D.S 0.1 1P; Hybrid with ~50% CNC; pure CNF DS01 1p. Top row samples were made with 0.6% dry weight, Bottom row with 0.2% dry weight.
BACKGROUND OF THE INVENTION
Introduction
Alongside the need of perceptual change in global production and consumption systems (McDonough and Braungart 2002) emerging interdisciplinary research practices stimulate the development of sustainable materials by employing organisms as biological fabrication systems (Camere and Karana 2018). These integrations extend the responsibilities of both scientists and designers and require cross-disciplinary collaborations, respectively. In the current study, a multidisciplinary exploration process enabled us to integrate advanced bio-fabrication technologies (Groll et al. 2016)within a sustainable industrial design research practices, and vice versa. This methodological approach enabled fundamental understanding of the material to envision, adapt, and illustrate unique properties, implications, and production scenarios, focusing on usability and environmental aspects of the product (Niaounakis and Niaounakis 2015).
Few years ago much of the knowledge in this scope was restricted by commercial companies (see for example Ecovative), yet during the last few years the commercial and academic interest constantly grows (Cerimi et al. 2019), with anincreasing number of academic groups from diverse disciplines that explore and develop mycelium-based composites (Appels et al. 2018; Haneef et al. 2017; Islam et al. 2017; Jones et al. 2018), expanding the knowledge regarding its fabrication possibilities, existing and potential properties, to promote alternative industrial products with circular production scenarios (Meyer et al. 2020).
In nature, white-rot fungi mycelium develops on dead wood, dispersing within and around it, preferentially decomposing lignin while leaving much of the cellulose intact (Figure 3). The fungal cell wall is composed of a dynamic and heterogeneous interwoven mesh of chitin, glucans, glycoproteins, and other polysaccharides [Bowman & Free, BioEssays2006, 28:799-808; Kang et al., Nat Commun 2018, 9:2747], creating interconnected networks, which together provide the properties required to withstand high internal hydraulic pressures, provide physical protection, and maintain internal humidity that is essential for fungal development. These properties play an important role when mycelium is employed as a structural material.
Figure 3: The fungal mycelium. From left to right: Illustration of fungal mycelium, comprising the fruiting body of the fungi (a mushroom) and the vegetative network below the surface (from Life, The Science of Biology, 10th ED); Mycelium on pine woodchips found in nature; A 3mm mycelium inoculum disk dispersing on woodchips in the lab, under sterile conditions; HR-SEM image depicting mycelium within a wheat straw plant cell.
So far, most of the intellectual property and academic study in the emerging field of mycelium-based composites was mainly focused on incubation of mycelium with plant-chips, sourced from regional agricultural and forest pruning residues that currently do not have practical discarding solutions (Cerimi et al. 2019; Elsacker et al. 2020; Jones et al. 2017; Meyer et al. 2020). The initial part of our research explored the potential uses of mycelium-woodchip biocomposites for sustainable industrial design applications, using regional forest and agricultural wastes. One fundamental finding was that the mycelium is generally hydrophobic on its external areas; thus, it decreases the hydrophilic nature of the woodchips, commonly resulting in amphipathic water-interface properties. This finding established the scope for the second part of this study, that focused on exploring the potential of a bio-nanocomposite hybrid material made of mycelium and nanocellulose, presuming that an integration of these materials would produce resilient films with improved the water resistance.
The invention presents and includes composite materials that comprise mycelium in combination with plant-derived substances such as cellulose and/or cellulose-based materials. Our study explored the potential integration of the two forest-based materials, fungal mycelium and nanocellulose (NC) using submerged culture growing method. This is a commonly used method for industrial production of fungi, in which mycelium may be grown in enriched liquid broth with desired conditions, forming macroscopic hyphal aggregates, which are then processed to extract different microbial products [Papagianni, Biotechnol Adv 2004, 22:189-259]. In the current approach, the mycelium incubation is accompanied by the addition of NC to the liquid broth. These bio-based materials are exceptionally promising for sustainable industrial applications as they can be readily processed into applicable materials with versatile range of properties using similar infrastructure, tools, and methods of paper processing to produce materials such as films or sheets for packaging with valuable mechanical performance and barrier properties to oxygen, grease, UV, and humidity.
We found that white-rot mycelium grown in a liquid culture that includes growth nutrients and nanocellulose (CNC, CNF) incorporates the nanocellulose within its filamentous structure to give a mycelium-nanocellulose biocomposite hybrid. Generally, the strength of the mycelium is improved by the inclusion of nanocellulose and the surface properties of the resulting film are dominated by the mycelium, which is more hydrophobic and essentially coats and integrates within it the nanocellulose elements. This 1-step bio-fabrication of a mycelium-nanocellulose nanohybrid material gives materials that can be processed in the ways familiar to papermaking, are water-resistant, thermally stable, mechanically robust, and potentially anti-bacterial and anti-fungal. Of all the NC types tested (enzymatic CNF, carboxymethylated CNF, CNC), carboxymethylated CNF gives an increase in the yield of mycelial mass, all else kept equal. Lastly, simply adding nanocellulose to mycelium does not produce a uniform material, so the inclusion of nanocellulose in the growth medium is a key element.
Several analysis methods (XPS, POM, HR-SEM, FTIR, AFM, contact angle), supports the conclusion that in the invented material, NC (nm-scale and otherwise) is fully absorbed, interlaced, and engulfed by mycelium, and potentially integrated within the hyphal cells, respectively affecting physio mechanical material properties. This observation is perhaps most visually evidenced by POM, where the non-birefringent rippled hyphal network appears superimposed over the NC (see Attias et al. 2020). This observation was consistent across all NC types employed in this study, although their sizes, nano-yield, morphologies, and charges differed significantly. Furthermore, evidence was provided to support the assembly and integration of the NC nano-fraction within the hyphal cell walls and not simply aggregated onto the cell wall exterior as evident in studies that use mycelium to take in ions from the liquid media to form nanoparticles. In fact, we did not find any study that demonstrates an incorporation of nanoparticles into the fungal pellet/ cell wall.
Mycelium liquid culture is already quite straightforward and scalable fabrication process, however the main innovation is the addition of nanocellulose to the growth medium, by replacing the distilled water ingredient with NC in varied wt%, to produce an integrated NC-mycelium biocomposites with hybrid properties. Mycelium-nanocellulose bio-composites can be processed in the ways familiar to nanocellulose or mycelium-based composites, such as vacuum filtration, standard molding, 3D pulp molding, 3D printing, spraying, freeze dry etc. The results of our study suggest that a family of differentNC-mycelium bio-composites can be readily achieved by varying NC content and type, incubation time, nutrient profile, fungal species, growth conditions and material processing methods, with a potential to tailor diverse materials depending on the desired application of interest. Notably, we found that carboxymethylated CNF gives a higher yield of the mycelial mass and that the dewatering stage of a mycelium-NC hybrid is faster compared to pure NC processing.
Figure 4: The selected fabrication approach. (A) Inoculation of mycelium pieces with nutrients and nanocellulose in sterile conditions; (B) Incubation at 25°c, agitated at 120RPM speed; (C-D) Following incubation, the material develops as a spherical pellet surrounded by a broth. The growth process is terminated by heat treatment. (E) The mixture is homogenized, dialyzed or centrifuged to remove residual nutrients. (F) The diluted mixture is used to make films - by vacuum filtration and drying under tension using customized cleaves. (G) Aerogels are made using freeze-drying of a diluted homogenized liquid mixture.
The following studies show that different fungal species, substrates, and approaches have been used to produce biocomposites with distinct properties. Space-filling composites produced from the solid-state cultivation of Trametes versicolor, Trametes ochracea, or G. sessile with various substrates from agricultural waste presented different characteristics depending on the fungus-substrate combination [Attias et al., J Clean Prod 2019, 119037]. Films from G. lucidum or Pleurotus ostreatus were stiffer when grown from a feeding substrate composed of microcrystalline cellulose (MCC) than of a mixture of MCC and easier to digest potato dextrose broth [Haneef et al., Sci Rep 2017, 7:41292].
Sun et al. [Sci Rep 2019, 9:3766] describe composites based on wood and mycelium, with cellulose nanofibrils (CNFs) added as a binder; and reports that growing mycelium on the wood and then adding CNFs resulted in enhanced physical and mechanical properties, such as reduced water absorption, as compared with physically mixing wood, mycelium, and CNFs.
U.S. Patent Application Publication No. 2011/0268955 describes a method of forming a molded part using a mixture of a fungal inoculum and a liquid aggregate, with homogenously distributed nanoparticles, such as nanoclay, nanocarbon fiber or metallic nanoparticles. The mixture is inserted into a mod cavity and live mycelium is grown to fill the cavity.
Additional background art includes Appels et al. [Sci Rep 2018, 8:4703]; Appels et al. [Commun Biol 2020, 3:334]; Grimm & Wosten [Appl Microbiol Biotechnol 2018, 102:7795-7803]; Jones et al. [Biomacromolecules 2019, 20:3513-3523]; Nawawi et al. [Compos Sci Technol 2020, 198:108327]; U.S. Patent Application Publication No. 2017/0218327; and International Patent Application Publication WO 2019/170355.
SUMMARY OF THE INTELECTUAL PROPERTY OF THE INVENTION
In our study we produced a new process and new sustainable mycelium-based material, in a single bio-fabrication step via an organic self-assembly (biofabrication) process, where nanocellulose (NC) becomes intimately integrated within the mycelial network, as opposed to being simply mixed with the mycelium post-growth (e.g., as described by Sun et al. [Sci Rep 2019, 9:3766]). The fungal mycelium is incubated alongside standard nutrients and NC under agitated liquid culture conditions to produce a homogeneous network structure comprising both mycelium and the NC. The properties of the obtained material may be modulated by the nature of the assembly and the final material composition, or other methods such as genetic modifications, biochemistry interventions or simple post-processing steps such as heat pressing.
The added substance may optionally comprise cellulose (e.g., in a form of fibers and/or nanoparticles such as CNCs or CNFs), and/or nanoparticles comprising a polymeric substance other than cellulose, such as polysaccharides (e.g., hemicellulose), polypeptides (e.g., silk), and/or synthetic polymers (e.g., polyester, nylon), or wood-based mass such as plant-chips wastes.
In contrast to some previously described mycelium-based biocomposites, which combine fungal inoculum with solid biomass such as woodchips [Attias et al., J Clean Prod 2019, 119037; Jones et al., J Bionanoscience 2017, 11:241-257; Girometta et al., Sustainability 2019, 11:281], in the approach described here, an added substance is co-incubated with mycelium in a liquid state, providing advantages of efficient integration of the mycelium and non-mycelium components, resulting in a versatile liquid mass. This liquid may be used as is, for example, to be dried into sheets or films. Post processing may be applied by pressing (e.g., by hot press); Processing may optionally be applied locally to alter properties of a selected region (e.g., enhanced permeability by perforation or reduced permeability by hot press). The hybrid liquid material may be used like paper and/or to coat another material, (e.g., by vacuum and/or by spray drying);
The liquid mixture may be 3D-printed (e.g., by multi-component 3D-printing); or applied as coating for textile fibers (e.g., by bath coating), which can be further processed using 3D textile knitting technics. Aerogels produced by freeze-drying may be used as a foam for varied applications. In any chosen fabrication method, various types of mycelium-based hybrid materials may be obtained by varying content and type of the second substance, fungal species, growth conditions, and/or material processing and post-processing approaches.
The resulting hybrid materials could be regarded as a modified form of mycelium, where the second substance (e.g., NC) incorporated within the mycelium results in modified properties such as enhanced mechanical strength. Alternatively, or additionally, hybrids comprising cellulose may be regarded as a modified form of cellulose (e.g., NC), whereby the mycelium covering the cellulose results in modified properties, such as enhanced water resistance. Thus, such hybrid materials may optionally be used in mycelium-oriented applications or embedded in existing manufacturing systems of the added substance (e.g., NC, pulp fibers).
Notably, our study uncovered that substances such as carboxymethylated cellulose can surprisingly enhance the yield of mycelium. Such enhancement of mycelium growth may be utilized when preparing hybrid materials such as described here, as well as when growing fungi for any other industrial purpose (e.g., for bioremediation; for agriculture; for biosynthesis of metabolic products such as antibiotics, proteins, exopolysaccharides; and/or for biomedical products and supplements).
Another outstanding finding is that the integration of NC with mycelium improved processing efficiency, by preforming much rapidly dewatering during the vacuum-filtration step of nano-paper processing. The processed hybrid slurries also resulted in nano-papers that were more resistant to swelling in water compared to pure NC materials.
We are currently processing barrier properties, which are expected to shed some more light on the application of the material and other potential customers. The ability of films to serve as a barrier against oils is a useful property (e.g., for packaging material of various food products). According to the initial analysis, all the tested films were detected as good oil barriers. (non-published data, expected to be processed and published in the following months). These results indicate that hybrid materials described here may serve as barriers to hydrophobic substances, in addition to being more water resistant than pure NC, thus may be useful, for example, as sustainable packaging materials for a variety of food products. Oxygen and humidity barrier properties are being tested as well.
In addition, the hybrid may also be processed co-incubation of mycelium, NC and a macro-scale solid biomass (e.g., woodchips, saw dust, or pulp fibers) to give a space-filling mycelium-based biocomposite that is strengthened by the inclusion of the NC through incubation. Such material may offer a sustainable alternative to a variety of Styrene products for physical and thermal and insulation applications. Through this study we developed an original useful with great sustainable and commercial potential implications. Using the space filling composites for agricultural applications. For example, to produce multi-cell trays for plants (known as seedlings trays, currently made of EPS); a tree protector (a tubular structure used for surrounding young trees in commercial tree plantations, root trainers or aerated containers that promote air trimming of the roots for improved yield and healthy plant development, and/or a tile-like structure for covering the ground adjacent to a tree, mainly used in urban horticulture. Space filling materials should also be applied for as soft-engineering elements, to hold soil, water or for bioremediation performances.
SUMMERIZED NOVELTY HYLIGHTS
- A novel material - NC is integrated within the fungal cellwall, to give hybrid properties.
- The NC (nanoparticles or nanofibers of various types and scales) is fully absorbed from the liquid medium and engulfed within the fungal mass during co-incubation with mycelium, to produce hybrid fungal pellets. We did not find other descriptions for absorbance and integration of NC or other nanoparticles by fungi in the literature.
- The addition of carboxy-CNF to the liquid medium increases the total mycelium yield.
- The coverage of NC by mycelium in the co-incubation process reduces interface incompatibilities and is a promising NC modification approach for its incorporation as an inherent strengthening additive in mycelium materials. Additionally, the hybrid nano-papers are more resistant to swelling in water compared to pure NC materials.
- The hybrid slurries more rapidly dewater than pure NC, improving the industrial yield of nano-papers production process.
COMMERCIAL POTENTIAL OF THE INVENTION
As petroleum-based plastics are increasingly avoided or even rejected in response to environmental concerns and societal pressure, (Dauvergne 2018; Xanthos and Walker 2017) the use of forest-based resources to address modern material demands is expected to continue to grow.(Kangas 2019; Lovrić, Lovrić, and Mavsar 2020; Näyhä 2019) Packaging is a high-volume area that stands to be improved by new advances in pulp and paper research that utilize bio-resources in place of traditional plastics to meet different barrier needs.(Helanto et al. 2019; Hubbe et al. 2017; Reddy et al. 2013; Reichert et al. 2020) Innovation is needed to support the pulp and paper sector as it transitions toward a bio-based circular economy, with efficiency, sustainability, and new materials predicted as the main value drivers in 2030. (Pätäri et al. 2016; Toppinen et al. 2017). The use of mycelium-based biocomposites is thus expected to increase sustainability while reducing the work, the wastes, and the costs involved in huge industries such as the paper industries, commercial forestry, furniture, packaging (food or other deliverables) textile, hygiene, bioremediation, packaging, and antimicrobial materials and surfaces.
Our current focus is on companies that are looking toward biobased, non-toxic packaging solutions, as the materials are fibrous and can be processed like paper to give paper-like materials with new properties. The applied sheets could be processed to produce a food tray or a replacement for conventional paper packaging with the added advantage of mycelium to make the material more hydrophobic, a grease barrier and easier to process because of the faster dewatering rate, while avoiding the use of hazardous chemicals. This invention is potentially interesting across a range of industries. Companies such as Ecovative could be interested in this material. Ecovative dominates the patent landscape around mycelium materials. Other smaller players that are looking into alternative meat and leather alternatives or nutritional additives may also be interested in this technology as mycelium is an emerging material in these areas. Another significant feature of our invention is the higher yield of the mycelial mass achieved through co-incubation with carboxymethylated CNF, that could be useful for the general production of fungal sourced metabolites such as EPS (exopolysaccharides), antibiotics, enzymes etc for biomedical products and supplements.
This study has contributed to advance, deepen, and engage the scientific understanding of mycelium material possibilities through a genuine methodology that integrate biotechnology with inclusive, circular design thinking that considers the overall life cycle of a product. including renewable resources, waste-streams, biodegradation, user scenarios, user preferences engaging beneficial biotechnological innovation possibilities through applied circular products. This approach is significant to confront with the constant increase of single used products within all areas of contemporary reality.